ONBOARD® evaporates liquid contaminants through its patented technology. It does not store them.
ONBOARD® Performance
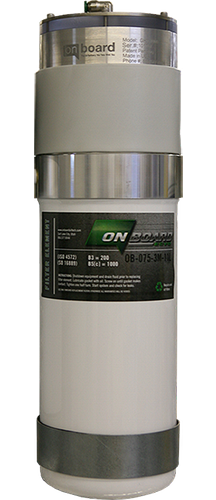
The ONBOARD® patented technology renders water, unburned fuel, and glycol from your engine-oil into a vapor, mixes the vapor with blow-by gases vacuumed from your crank case, and delivers the combined vapors back through the intake for re-burn.
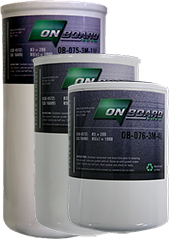
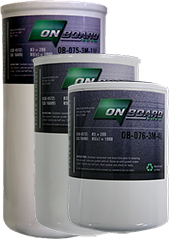
Why ONBOARD®?
The ONBOARD® System takes oil filtration to a new level, leaving every other product literally in the dirt. Diesel engines have high compression which leads to increased blow-by contaminants entering the crank case. These intruders include soot, unburned fuel, and water from combustion and condensation. These contaminants adversely affect the oil causing increased nitration and oxidation as well as adverse viscosity changes. As the process is prolonged, the contaminants degrade your oil’s ability to protect your engine. The ONBOARD® System filters the particulates while the vacuum chamber evaporates, through convection, the liquids from the motor oil while the engine is running, thus ensuring maximum oil lubricity and ultimate protection for your precious equipment.
ONBOARD®: a two-stage system:
Stage I – The Particle Filter
Standard, full-flow OEM oil filters remove particles no smaller than 20µ at a nominal rating. If the OEM filter did remove smaller particles down to 3µ, the filter would soon become clogged, increasing oil pressure to the point of opening the pressure relief valve and allowing unfiltered oil to circulate throughout the engine. Not good. The ONBOARD® Particulate Filter removes 99.99 % of particles larger than 2µ. This G8 Beta 1000 dual-glass filter element is an integral part of the ONBOARD® System, and can help extend engine life well beyond 60% with our particle filter alone…
Stage II – Vacuum Dehydration
However, we do not stop with particle filtration. What truly separates ONBOARD® from the old school filtration systems is our Evaporation Convection - Vacuum Dehydration technology. After passing through the Particle Filter, the motor oil flows into the Vacuum Dehydration chamber where water, unburned fuel, and glycol, are first evaporated, then vacuumed back through the intake for re-burn in the combustion chambers. Thus, the engine itself is actually an integral part of the refining process!
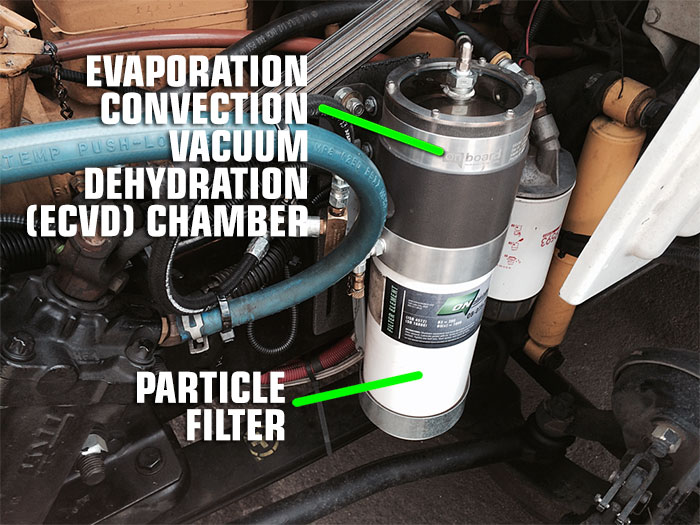
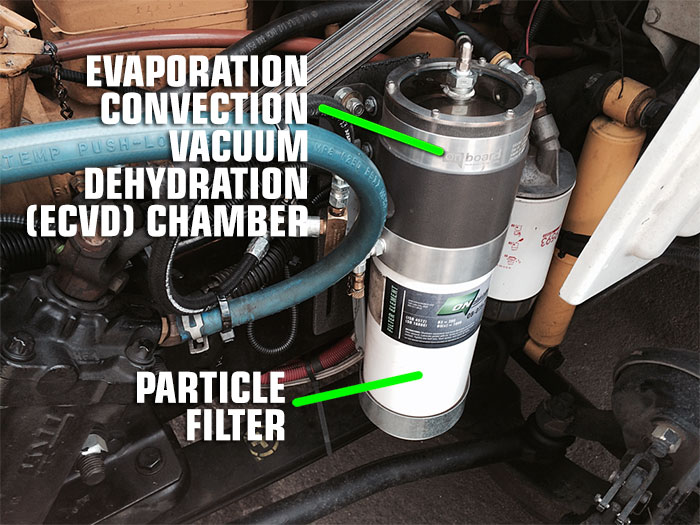
The ONBOARD® Advantage
The scheduled maintenance industry has been working tirelessly to remove particulates to extend the life of motor oil with admirable results. However, the endless, equipment-destroying issue of liquid contaminants in the lube oil has been nearly impossible to truly eradicate.
Numerous systems have attempted to trap and hold water, unburned fuel, and glycol in their cellulose, paper, or wood filters. They were, and still are simply unable to hold more than a limited amount of these merciless, acid-generating, viscosity-altering, liquid poisons found in the motor oil.
The ONBOARD® System erases liquid contaminants from existence, while the engine is running. This simple, passive process keeps your engine running with TRULY clean oil every minute, every mile.
We have created a product that decreases fuel consumption by decreasing friction, that avoids polluting soil and water and, if possible, preserves air quality. In addition we wanted to cut operators’ costs. Our product presents a cheaper, simpler, smaller and more convenient way to maintain an engine.
Oil never loses its lubricity—its lubricating capacity. It becomes contaminated with particles and liquids like water, fuel and chemicals.
ONBOARD® has created a product that truly refines motor oil while the engine is running. The ONBOARD® System increases fuel efficiency, decreases soil and water pollution, and preserves air quality. In addition, our goal is to cut operator’s costs. ONBOARD® presents a simpler, smaller, and far more convenient system for maintaining your engine.
Key Benefits
The ONBOARD® System will perform the following list of benefits for your engine or fleet.
- Refines oil while engine is running
- Eliminates liquid contaminants
- Increases fuel efficiency
- Mitigates fuel dilution of motor oil
- Extends DEF yield
- Reduces DPF regen cycles
- Maintains 100% oil lubricity
- Reduces downtime and costs
- Increases oil change intervals
- Saves your money
- Reduces waste oil production
- Prolongs engine service well beyond 60%
- Huge return on investment
- Reduces hydro-carbon impact
- Implementation is simple!
Compatibility
The ONBOARD® System is compatible with virtually all internal combustion engines.
- Caterpillar
- Cummins
- Detroit Diesel
- Ford
- General Motors
- International
- Isuzu
- John Deere
- Kohler
- Komatsu
- Mack
- MAN
- Mercedes Benz
- Mitsubishi
- Onan
- Perkins
- Scania AB
- Volvo
- Yanmar and more...
Implementing ONBOARD® Performance Products will dramatically advance your company’s quest to attain maximum sustainability while at the same time, bring an astounding increase to your bottom line. There is far too much at stake to ignore the real opportunity of ending your production of waste oil while improving the lifespan and operations of your fleet.
It Takes a New Perspective
Many consider environmental initiatives in terms of fuel mileage, but the elite know there is much more they can be doing to protect the environment and earn credibility. Astute organizations are aggressively seeking out additional technologies that can affordably help them minimize negative effects to the environment, and if improving their bottom line comes with it, AMAZING! The ONBOARD® System drastically reduces oil consumption and the environmental risks associated with the dangerous responsibility of handling waste oil. As ONBOARD® expands its reach, the reduced carbon chain is compounded significantly.
ONBOARD® Environmental Benefits
- Increased sustainability
- Reduced hydro-carbons
- Reduced oil consumption
- Reduced waste oil production
- Reduced exhaust vapors
- Reduced filters in the landfills
Increased Fuel Efficiency
Clean oil is crucial to the proper operation of large diesel and CNG engines. Dirty oil causes additional friction requiring extra fuel to compensate. ONBOARD® customers have been reporting fuel savings ranging from 8-13%.
ONBOARD®’s Patented Technology Dramatically Increases Efficiencies
The ONBOARD® System uses crankcase gases to complete the evaporation and convection process. The vapors are not released to the atmosphere, but instead are re-burned in the combustion chamber. This process reduces the carbon build up in the combustion chamber and soot and fuel dilution are virtually eliminated.
A large step to reduce the oil consumption and its impact on the environment can begin today if everyone becomes aware of their ability to contribute by adopting a supplementary oil filtration system such as the ONBOARD® System. As ONBOARD® expands its reach, the reduced carbon chain is compounded significantly.
It’s a fact. The ONBOARD® Products Help Preserve The Environment
Let’s consider how the ONBOARD® System works.
ONBOARD® Particle Filters utilize the latest generation of G8 dual-glass filter elements capable of eliminating particles from your engine’s oil down to 3µ in diameter. Standard full-flow oil filters only remove particles down to 20µ in size, but studies have shown that over 60% of all engine wear is caused by particles in the 5µ to 20µ range. The dirt-free oil is kept at operating temperature in the ONBOARD® Fluid Filter where the fuel dilution, water and liquid contaminants are evaporated and discharged sending completely clean oil back to the engine. The continuous repetition of this cycle keeps your oil clean, increases fuel economy, increases the life of the engine and eliminates the steady production of waste oil, thus reducing all the negative environmental impact associated with frequent oil changes.
Reducing Our Oil Consumption
The United States accounts for 26% of the world’s consumption of lubricating oils.
Economic growth in developing countries is spiking the demand for lubricating oils. Left unchecked, this trend will surely contribute greatly to the contamination of the Earth’s environment.
It is estimated that the United States consumes about 2.8 billion gallons of oil per year. If everyone used bypass oil filters like the ONBOARD® System, the consumption would drop by about 2.3 billion to around 500 million gallons per year. A monumental step to reduce oil consumption and its impact on the environment can begin today if everyone becomes aware of their ability to contribute by adopting the ONBOARD® System. The positive impact on the environment due to the reduction of the consumption and reduction of waste oil would undeniably benefit the environment.
With only 14% of waste oil being recycled, it is our responsibility to drastically improve this number. ONBOARD® Performance Products drastically reduce oil change intervals and subsequently reduces waste oil.
Reducing Filters in the Landfills
The disposal of oil filters has become a concern for state governments across the country.
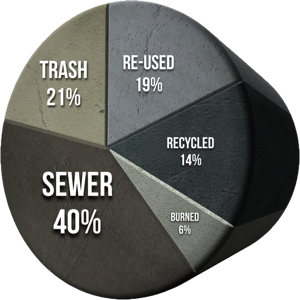
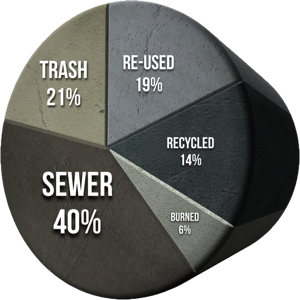
Did you know that one gallon of improperly disposed of oil can render a million gallons of water undrinkable? That’s a high price to pay. This graph shows where waste oil goes now.
Oil filters contain on average, more than 10 fluid ounces of used motor oil, even after draining. Recycling programs have been established across the country to reduce the amount of filters going to the landfills. Some states including California, North Carolina and Wisconsin have recently banned or are in the process of banning oil filters from landfills. California alone generates 67 million used automotive filters per year.
Vehicles using the ONBOARD® System would also reduce the number of regular full-flow filters going into the landfills. Filters are generally changed at every oil change and high mileage vehicles can expect 8 to 15 filter changes per year. Under normal conditions, with the ONBOARD® System you would only replace 3 to 4 ONBOARD® Particle Filters and one full-flow filter per year.
Related Government Studies
- PDF | The State of California EPA certifies that oil bypass filtration is a pollution prevention technology and is also certified by the DTSC.
- PDF | The General Accounting Office did a 3 year study to find that the SAE study was proven correct as their study concluded positive results.
- PDF | The state of North Carolina EPA Study mentions oil filters are banned from landfills.
Implementing the ONBOARD® System will dramatically advance your company’s quest to attain maximum sustainability while at the same time, bring an astounding increase to your bottom line.
Get ONBOARD® and reduce your carbon footprint!
ONBOARD® XD
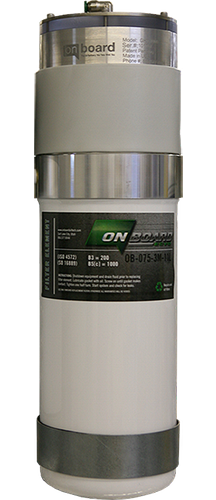
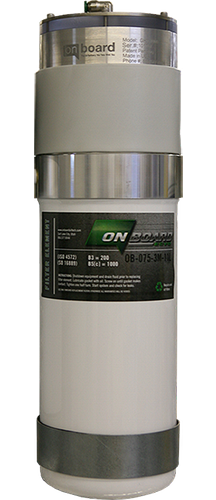
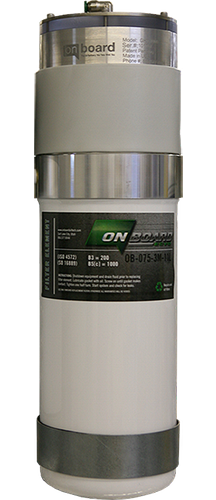
The ONBOARD® XD features a heavy-duty mounting bracket to withstand even the roughest off-road terrain.
The ONBOARD® XD System
Applications
To be used on all Diesel and CNG engines used in Municipality Fleets, Trucking, Construction, Mining, Utility Services, Agricultural, Power Generation, Marine and Heavy Industrial uses.
ONBOARD XD Gallery
Five Easy Connections
- Oil pressure feed line from pressure port to unit.
- Oil drain-back hose from the ONBOARD Chamber back to the oil sump via oil fill tube, valve cover, oil pan fitting, casting plate fitting, oil drain plug, etc.
- Vacuum line from the ONBOARD Chamber through an oil separator filter to the intake airline between the air filter and the cold side of the Turbo.
- Crank case vent line from the oil cap, oil fill tube, valve cover, PCV access, etc.
- 12v or 24v keyed power and ground connection for the ONBOARD heater. Oil does NOT touch the heating element. Heater is to keep the oil at operating temperature (193º), in the ONBOARD Chamber.
Standard Installation Kit Includes:
- ONBOARD® XD Refiner
- Hose Clamps
- Fittings for Drain Oil and Crankcase Connections
- Inline Fuse
- Vacuum Connection
- Oil Pressure Shutoff Valve
- Flow Meter and Oil Sample Valve
- Auxiliary Bracket
Deluxe Installation Kit
- Coming soon
NOTE: Due to different engine applications, there may be additional components required. You can be assured that you will receive support throughout the installation process.
OEM full-flow filtration is based on a nominal rating verses absolute. Particulates larger than 5µ cause wear to turbo bearings. ONBOARD® removes particulate greater than 3µ from the lubricant using a Beta 1000 G-8 Dual Glass media which is 99.9% Absolute. This is the highest quality filtration media on the market today.
Service Intervals
The ONBOARD® Particulate Filter should be replaced every 20-50,000 miles or 300-450 hours unless noted by your oil analysis report. Regular oil samples are suggested to ensure that the oil is maintaining lubricity and tests within the OEM guidelines. The full-flow filters are to be changed at 20,000 miles or once per year.
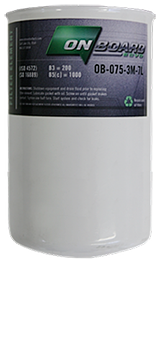
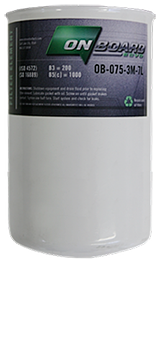
7" Particle Filter
OBF-075-3M-7L
- Good for up to 20-30,000 miles or 300-400 hours
- For engines with oil sump capacity 16-32 quarts
- Utilizing the best filtration media in the industry
- G-8 Glass media Beta 1000 rating at 3µ 99.99% Absolute (not nominal)
Compatibility is universal.
The ONBOARD® XD System is compatible with virtually all internal combustion engines.
- Caterpillar
- Cummins
- Detroit Diesel
- Ford
- General Motors
- International
- Isuzu
- John Deere
- Kohler
- Komatsu
- Mack
- MAN
- Mercedes Benz
- Mitsubishi
- Onan
- Perkins
- Scania AB
- Volvo
- Yanmar and more...
ONBOARD® LD
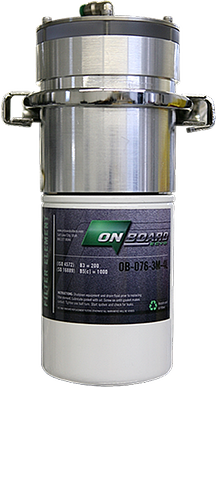
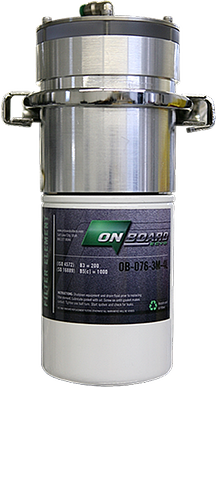
The ONBOARD® LD features a heavy-duty mounting bracket (pictured).
Applications
To be used on Unleaded, Diesel and CNG engines for Personal Transportation, Delivery, Light Duty Vehicles, Forklifts, Mobile Power Generation, Taxi Services, Small Buses, Small Intercity Service Trucks/Vehicles, Municipality Fleets.
ONBOARD LD Gallery
Five Easy Connections
- Oil pressure feed line from pressure port to unit.
- Oil drain-back hose from the ONBOARD Chamber back to the oil sump via oil fill tube, valve cover, oil pan fitting, casting plate fitting, oil drain plug, etc.
- Vacuum line from the ONBOARD Chamber through an oil separator filter to the intake airline between the air filter and the cold side of the Turbo.
- Crank case vent line from the oil cap, oil fill tube, valve cover, PCV access, etc.
- 12v or 24v keyed power and ground connection for the ONBOARD heater. Oil does NOT touch the heating element. Heater is to keep the oil at operating temperature (193º), in the ONBOARD Chamber.
Standard Installation Kit Includes:
- ONBOARD® LD Refiner
- Hose Clamps
- Fittings for Drain Oil and Crankcase Connections
- Inline Fuse
- Vacuum Connection
- Oil Pressure Shutoff Valve
- Flow Meter and Oil Sample Valve
- Auxiliary Bracket
Deluxe Installation Kit
- Coming soon
OEM full-flow filtration is based on a nominal rating verses absolute. Particulates larger than 5µ cause wear to turbo bearings. ONBOARD® removes particulate greater than 3 microns from the lubricant using a Beta 1000 G-8 Dual Glass media which is 99.9% Absolute. This is the highest quality filtration media on the market today.
Service Intervals
The ONBOARD® Particulate Filter should be replaced every 8-10,000 miles or 250-350 hours unless noted by your oil analysis report. Regular oil samples are suggested to ensure that the oil is maintaining lubricity and tests within the OEM guidelines. The full-flow filters are to be changed at 20,000 miles or once per year.
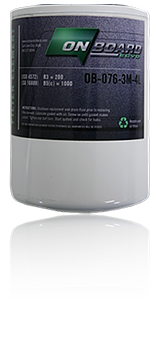
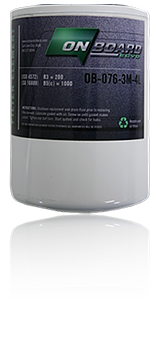
Replacement Particle Filters
- 4" Particle Filter
- Part: OBF-076-3M-4L
- Good for up to 8-10,000 miles or 250-350 hours
- For engines with oil sump capacity 4-16 quarts
- Utilizing the best filtration media in the industry
- G-8 Glass media Beta 1000 rating at 3µ 99.99% Absolute (not nominal)
The ONBOARD® LD System is designed for light duty diesel use.
Kits Available For:
Dodge RAM Cummins
- 2012 And Earlier Call For Details
- 2013-2015 Dodge Cummins Call For Details
- Dodge 5.9L Cummins Call For Details
Chevrolet Duramax
- Chevy/GM Duramax 2500-6500 Call For Details
Ford Diesel
- Ford 6.7 Liter Call For Details
- Ford 6.4 Liter Call For Details
- Ford 6.0 Liter Call For Details
- Ford 7.3 Liter Call For Details
Gearhead Oil Analysis
View Sample Oil Report
1. Extract
Using provided clear bottle, extract engine oil from the receptacle mounted on the ONBOARD system and fill out the data label provided.
2. Send
Place oil sample in pre-paid shipping envelope, and send through US Mail. NO POSTAGE NECESSARY!
3. Receive
Gearhead Lab Tech sends detailed analysis report to you.
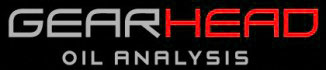
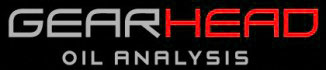
Tests include:
- Wear Metals
- Viscosity @ 100°
- Fuel Dilution %
- Soot %
- Water by Crackle %
- Total Base Number
- Oxidation / Nitration
Get started with Gearhead Now!
What is Oil Analysis?
Do you know oil tells a story and provides a working history of your equipment as well as the condition of your lubricant? With Gearhead Oil Analysis, you can get a look “inside” your equipment and get the story without costly teardowns or unnecessary lubricant changes. This can reduce maintenance costs as well as provide peace of mind knowing that your equipment is safe and not wearing out at an excessive rate.
Here at Gearhead Oil Analysis, we have many years of experience testing synthetic and petroleum lubricants. This allows us to provide quality analysis no matter which type of lubricant you use. Be proactive rather than reactive when it comes to protecting your investment. Oil Analysis can identify the four biggest engine killers before it’s too late! Routine testing can tell you where they come from and what they can do to your equipment.
Fuel Dilution is the amount of raw, unburned fuel that ends up in the crankcase. It lowers viscosity creating friction-related wear almost immediately. Dilution levels exceeding 8% could cause a crankcase explosion.
Soot is a sign of reduced combustion efficiency and is caused by over-fueling, air restrictions, blow-by, excessive engine brake use and/or excessive exhaust backpressure. Knowing that a particular engine design creates and retains more of it doesn’t make higher levels acceptable. Alarm limits should remain the same — maintenance practices should change
Coolant usually enters an engine through a broken head gasket seal, cracked cylinder head, cracked block, faulty water pump or lube cooler and can cause wear in bearings, bushings, pistons, liners, cams and valves.
Dirt is detected by the presence of silicon and aluminum. It causes wear most rapidly in components made of iron, lead, copper and tin, such as pistons, bearings and liners.
Routine testing can tell you where they come from and what they can do to your equipment.
ONBOARD® Oil and Fuel Estimated Savings Calculator
NOTE: Actual savings will vary due to age and condition of engines, driving habits, altitude, etc.
Once you populate all the fields in the first section you will see your estimated savings stack up below.
About ONBOARD® Performance Products
ONBOARD®’s patented Evaporation Convection Vacuum Dehydration process collects crankcase vapors combined with evaporated water, glycol and unburned fuel and delivers the contaminated vapor back to the combustion cycle for re-burn. Your diesel, CNG or gasoline engine is now an oil refiner working constantly to keep your oil in pristine condition. The results are unmatched by any other oil purification system available.
ONBOARD® will increase efficiencies, minimize oil consumption, reduce waste oil, improve fuel economy, and help conserve resources, and save you money! ONBOARD® is manufactured with the highest quality materials to ensure lasting service for your fleet and field equipment. It’s time to get on board with ONBOARD®. The ONBOARD® System is proudly manufactured in the USA!
Oil never loses its lubricity—its lubricating capacity. It becomes contaminated with particles and liquids like water, fuel and chemicals.