The ONBOARD® System removes contaminated gaseous vapors from the crankcase and collectively returns them to the combustion chamber for re-burn.
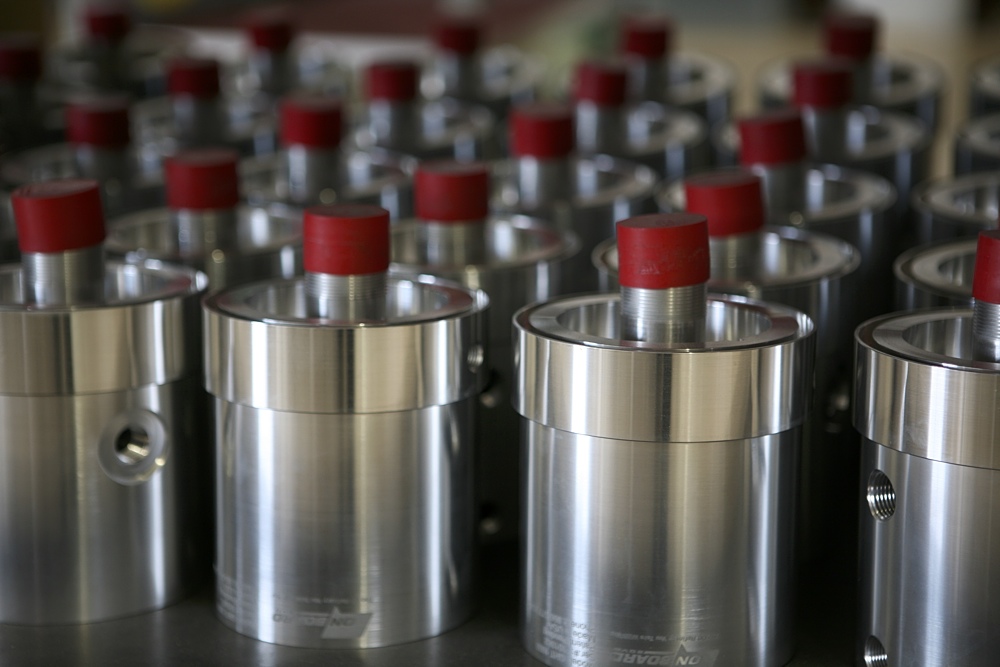
The ONBOARD® Assembly Line, Mesa AZ.
The ONBOARD® System is a disruptive technology that is committed to providing a cost-effective alternative to traditional oil changes. We are tireless in our mission to minimize oil consumption, decrease fuel consumption, reduce waste oil, increase efficiencies and conserve resources for our customers.
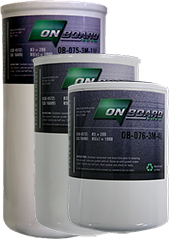
ONBOARD® Particle Filter
Whether you are an independent or are operating a diesel or CNG fleet, heavy-duty equipment, marine vessels or power generators, the ONBOARD® System will dramatically improve your bottom line by extending the life of your engine and drastically increasing the time between engine overhauls.
ONBOARD® prolongs the life of the engine oil by removing the contaminates.
The ONBOARD® Advantage
The ONBOARD® System’s process removes contaminated gaseous vapors from the crankcase and collectively returns them to the combustion chamber for re-burn.
The scheduled maintenance industry has been working tirelessly to remove particulates to extend the life of motor oil with admirable results. However, the endless, equipment-destroying issue of liquid contaminants in the lube oil has been nearly impossible to truly eradicate.
Numerous systems have attempted to trap and hold water, unburned fuel, and glycol in their cellulose, paper, or wood filters. They were and still are simply unable to hold more than a limited amount of these merciless, acid-generating, viscosity-altering, liquid poisons found in the motor oil.
The ONBOARD® System erases liquid contaminants from existence, while the engine is running. This simple, passive process keeps your engine running with TRULY clean oil every minute, every mile.
We have created a product that decreases fuel consumption by decreasing friction, that avoids polluting soil and water and, if possible, preserves air quality. In addition, we wanted to cut operators’ costs. Our product presents a cheaper, simpler, smaller and more convenient way to maintain an engine.
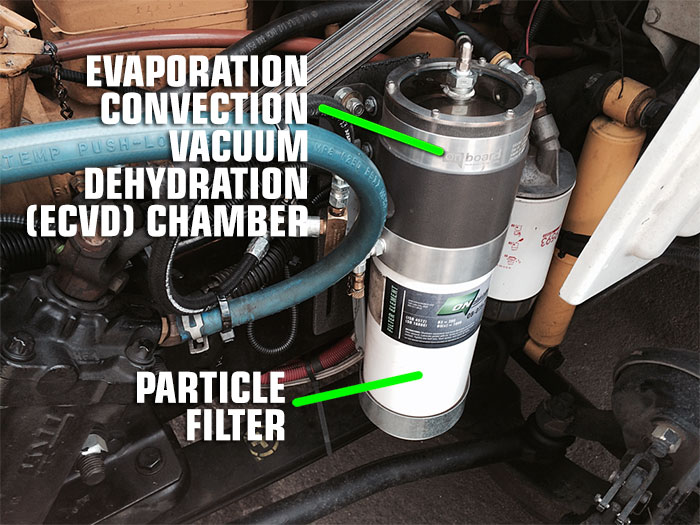
ONBOARD® utilizes a two-stage system.
ONBOARD® utilizes a two-stage system:
Stage I – The Particle Filter
Most Original Equipment Manufacturer’s (OEM’s) filter element blocks particles down to just 20µ. Because OEM filters are full-flow filters, if they removed particulates down to 3 microns, they would quickly clog and soon stop the flow of oil to internally lubricated parts. The ONBOARD® Particulate Filter removes 99.99 % of particles larger than 2µ. This G8 Beta 1000 dual-glass filter element is an integral part of the ONBOARD® System and can help extend engine life well beyond 60%.
Stage II – Vacuum Dehydration
What truly separates ONBOARD® System from the old-school filtration systems is our patent-pending vacuum dehydration technology. After oil passes through the Particle Filter, it moves to the chamber where water, fuel and other undesirable liquids evaporate and are vacuumed back through the intake for re-burn in the combustion chambers. Thus, the engine itself is actually part of the oil refining process!
Component Specifications
The ONBOARD® System Chamber
The evaporation and convection processes that extract water, fuel and other liquids from motor oil occur in the head unit of the ONBOARD® System, optimized by the unique design of the chamber.
The evaporation rate of contaminating fluids in oil will increase in proportion to the head unit’s surface area. Because water molecules need to be on the oil’s surface to evaporate, the greater the exposed surface, the faster the evaporation, With a larger area, more water molecules are on the surface of the oil, therefore, more water can evaporate. The evaporation rate depends on the environment of the liquids: temperature, humidity, amount of adjacent air and air movement. Convection, (the heat transfer of a gas or liquid by air current circulation and the phenomenon that makes water and fuel vapors rise and escape the oil), depends on the total surface area of the exposed liquid.
Unique Features
To enhance the evaporation convection processes, oil emerges at the top of a heated ramp and flows down to the bottom. The ramp is heated simply to keep the oil at operating temperatures in cold weather by a 12V heating unit located outside the chamber. The heating element does not contact the oil at any time.
Air from the crankcase is drawn into the vacuum chamber and blows over the oil flowing down the convection ramp. Evaporated fuel and water vapor rise, and the incoming air circulates out, taking the vapor with it. Water vapor and unburned fuel vapors return to the air intake of the engine for re-burn, adding to engine combustion rather than polluting the environment. Thus, the engine itself, with the unique ONBOARD® System, contributes to the oil-refining process.
The flow rate of oil in the ONBOARD® System will depend on 1) the oil pressure, which varies both in engine models and in their applications, and 2) the temperature and viscosity of the oil. In general, oil flow is estimated at 3-4 gallons per hour.
The ONBOARD® System chamber is fabricated in the USA from 6061 aircraft grade aluminum for maximum durability and strength while keeping weight to a minimum.
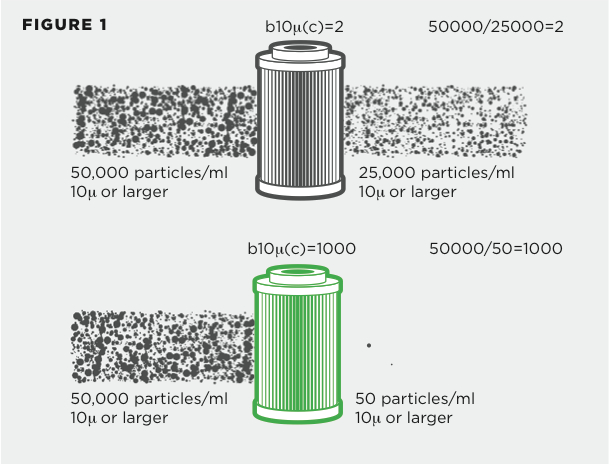
Figure 1: Illustrating the difference between absolute and nominal filter efficiency using a 10µ filter element. The ONBOARD® System utilizes a 3µ G8 dual-glass filter element. This quantifies contaminate capture retention at a Beta 1000 3µ 99.99% absolute.
Inside The ONBOARD® Particle Filter
The Particle Filter of the ONBOARD® System uses the latest generation of G8 glass elements. Glass media, compared with cellulose, is more compatible with hydraulic fluids, synthetics, solvents, and high-water-based fluids. Glass also has a significant filtration efficiency advantage over cellulose and is classified as absolute, whereas cellulose efficiency is classified as nominal.
The filter used by the ONBOARD® System uses an absolute 3µ, Beta 1000 element. Elements of different media with the same micron rating can have substantially different filtration efficiencies. Glass also has much better dirt holding capacity than cellulose.
Today’s industrial and mobile hydraulic circuits require elements that deliver specified particle filtration under all circumstances. Wire mesh supports the media to ensure against cyclical flow fatigue, temperature, and chemical resistance failures that occur in filters with synthetic support mesh.
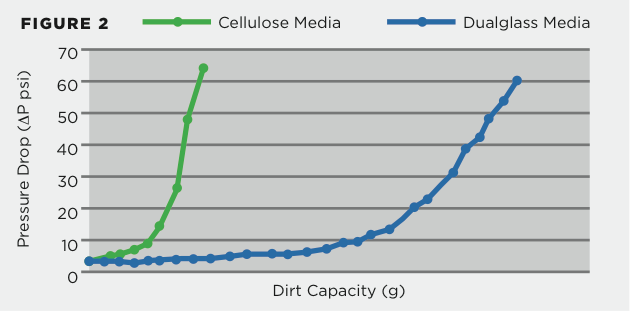
Figure 2: A glass element can last 4-5 times longer than a cellulose alternative.
ONBOARD® Heating Element
The ONBOARD® System uses a precision cartridge heater that provides localized heat to restricted work areas requiring close thermal control. The US-made heating element is below the outside surface for maximum heat transfer, minimum core temperatures, and faster heating. It is packed in magnesium oxide, rests on a ceramic element support and is covered by a Series 300 stainless steel sheath.