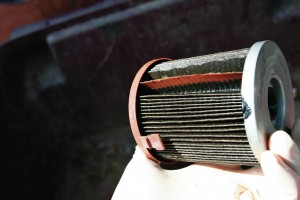
By Jim Fitch, founder and president, Noria Corporation
Glycol
Glycol enters diesel engine motor oils as a result of defective seals, blown head gaskets, cracked cylinder heads, corrosion damage and cavitation. One study found glycol in 8.6 percent of 100,000 diesel engine samples tested. A separate study of 11,000 long-haul trucks found severe levels of glycol in 1.5 percent of samples and minor amounts of glycol in 16 percent of samples. The following are some of the risks associated with glycol contamination:
- Just 0.4 percent coolant containing glycol in diesel engine oil is enough to coagulate soot and cause a dump-out condition leading to sludge, deposits, oil flow restrictions and filter blockage.
- According to one study, glycol contamination results in wear rates 10 times greater than water contamination alone.
- Glycol reacts with oil additives causing precipitation. For instance, an important anti-wear additive in motor oils, zinc dialkyl dithiophosphate (ZDDP), will form reaction products and plug filters when oil is contaminated with glycol. This leads to loss of anti-wear and antioxidant performance as well.
- Glycol has led to cold seizure of engines.
- Ethylene glycol oxidizes into corrosive acids, including the following: glycolic acid, oxalic acid, formic acid and carbonic acid. These acids cause a rapid drop in the oil’s alkalinity (base number), resulting in an unprotected corrosive environment and base oil oxidation.
- Oil balls (abrasive spherical contaminants) form from the reaction of calcium sulfonate detergent additives (found in nearly all motor oils) and glycol contamination. These balls are a known cause of damage to crankcase bearings and other frictional surfaces within an engine.
- Glycol contamination substantially increases oil viscosity which impairs lubrication and oil cooling.
Fuel Dilution
Frequent starts of an engine, excessive idling and cold running conditions can lead to moderate fuel dilution problems. Severe dilution (excess of two percent) is associated with leakage, fuel injector problems and impaired combustion efficiency. These are symptomatic of serious conditions that cannot be corrected by an oil change. According to one reference, 0.36 percent of total fuel consumption ends up in the crankcase. Problems associated with fuel dilution include:
- Diesel fuel dilution in cold operating conditions can cause waxing. During startup, this can result in low oil pressure and starvation conditions.
- Diesel fuel carries unsaturated, aromatic, pro-oxidant molecules into the motor oil. This can result in a premature loss of base number (loss of corrosion protection) and oxidative thickening of the motor oil, causing deposits and mild starvation.
- Fuel dilution can drop the viscosity of a motor oil from say, a 15W40 to a 5W20. This collapses critical oil film thicknesses, resulting in premature combustion zone wear (piston, rings and liner) and crankcase bearing wear.
- Fuel dilution from defective injectors commonly causes wash-down of oil on cylinder liners which accelerates ring, piston and cylinder wear. It also causes high blow-by conditions and increased oil consumption (reverse blow-by).
- Severe fuel dilution dilutes the concentration of oil additives and hence, diluting their effectiveness.
- Fuel dilution by biodiesel may result in higher than normal problems compared to diesel refined by crude stock. These problems include oxidation stability, filter plugging issues, deposit formation and volatility resulting in crankcase accumulations.
Soot
Soot is a by-product of combustion and exists in all in-service diesel engine motor oils. It reaches the engine by various means of blow-by during engine operation. While the presence of soot is normal and expected for a given number of miles or hours of service on an engine oil, the concentration and state of soot may be abnormal, signaling a problem with the engine and/or a need for an oil change. Following are some issues related to soot contamination:
- Combustion efficiency is directly related to the soot generation rate. Poor ignition timing, restricted air filter and excessive ring clearance cause high soot load. Combustion problems are not solved by an oil change.
- New diesel engines designed for lower emissions have higher injection pressures. This corresponds to increased sensitivity to abrasive wear (for example, from soot) between rocker, shaft and rocker bearing and can lead to rocker arm seizure. New exhaust gas recirculation (EGR) units on diesel engines amplify the amount and abrasive damage and soot production.
- Viscosity increases with soot load. However, high dispersancy associated with some modern engine oils may increase viscosity with soot even more. High viscosity corresponds to cold-start problems and risk of oil starvation.
- Soot and sludge in engines deposit or separate from the oil presenting risks to engine reliability including rocker boxes, valve covers, oil pans and head deck.
- Deposits on engine surfaces interfere with combustion efficiency and fuel/oil economy.
- Soot polishes off protective anti-wear soap films in boundary zones such as cam and cam follower zones.
- Carbon jacking from the buildup of soot and sludge behind piston rings in grooves can cause rapid wear of rings and cylinder walls. This can cause broken or severely damaged rings during cold-start conditions.
Water
Water is one of the most destructive contaminants in most all lubricants. It attacks additives, induces base oil oxidation and interferes with oil film production. Low levels of water contamination are normal in engine oils. High levels of water ingression merit attention and are rarely correctable by performing an oil change. The following are some additional notes on water contamination:
- Long idling in wintertime causes water condensation in crankcase, which leads to loss of base number and corrosive attack on surfaces, oxidation of the oil, etc.
- Emulsified water can mop up dead additives, soot, oxidation products and sludge. When mobilized by flowing oil, these globular pools of sludge can knock out filters and restrict oil flow to bearings, pistons and the valve deck.
- Water sharply increases the corrosive potential of common acids found in motor oil.
Failure Development Period
The failure development period can vary considerably for these contaminants. Most sudden-death failures from moderate levels of contamination will usually have one or more aggravating factors (the combo effect). Conversely, massive concentrations of one or more of these contaminants can result in sudden-death failures unaided by an aggravating circumstance. There are dozens of other aggravating factors that can drastically shorten the failure development period as well. More typical is when a moderate problem goes unnoticed and develops over time. This can shorten engine life from say, 750,000 miles to 300,000 miles.
The cumulative effect of oil contamination on engine reliability, fuel economy, exhaust stream emissions and maintenance cost of a large fleet is massive. There are no motor oil additives that control the damage caused by these contaminants. Therefore, proactive maintenance and oil analysis are critical strategies to counteract risks.
ONBOARD® was specifically designed to remove, through evaporation and convection, these damaging liquid contaminants from the motor oil while the engine is running.